PCGL has more than ten years experiences manufacturing virtually any type of printed circuit boards for your automotive applications. We strictly execute production and inspection in accordance with production requirements, and ensure that every automobile circuit board has zero defects.
PPAP (Production part approval process)
APQP (Advanced Product Quality Planning)
ISO 9001:2015
IATF16949:2016
ISO 14001:2015
UL certified
The following procedures we process for all the Automotive Boards.
1. Marketing department:
Understanding the uses and characteristics of customers' automotive products. Form a team dedicated to this product, including engineering, process and production, quality,etc.
2. Engineering department:
Reviewing customer data, compile production process, and identify special requirements from clients.
3. Production process department:
According to the production requirements provided by the engineering department, prepare special product operation instructions, and begin to prepare PPAP.
4. Production department:
Mark the product and label on the lot card. Each process has to be recorded.
5. Quality department:
Collect the data and confirm whether the product is qualified, and assist the process department to finish the PPAP and APQP.
6. Before the final delivery, PPAP and APQP will be submitted to the customer firstly. Clients confirms the file is OK or not firstly, and then delivers the product, waiting for the customer's final verification.
Types of Automotive PCBs
Flex PCBs – These boards are made of flexible plastic substrates. They are composed of PEEK, polyamide, or transparent polyester films. These boards can be twisted and bent. Find their applications around bends and corners in an automobile.
Rigid PCBs – The rigid boards are made of FR4. These boards aren’t flexible. They are usually found in display monitors and reverse cam screens.
Rigid-Flex PCBs – These are circuit boards are a combination of Rigid and Flexible boards. They are implemented in lighting systems.
HDI PCBs – These boards feature higher wire density per unit area, finer lines and spaces, and high pad connection density. The HDI boards accommodate more components and play a prominent role in miniaturization. These boards are widely used for infotainment systems.
LED PCBs – The LED boards made of aluminum substrate since they require heat dissipation. They can be found in car indicators, headlights, and brake lights.
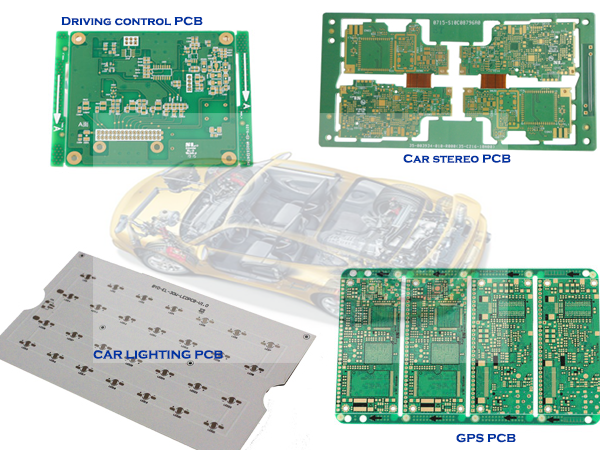